Comprehending the Fundamentals and Applications of Plastic Extrusion in Modern Manufacturing
In the world of modern-day production, the technique of plastic extrusion plays a crucial function - plastic extrusion. This intricate process, involving the melting and shaping of plastic with specialized dies, is leveraged across numerous industries for the production of varied products. From auto components to durable goods product packaging, the applications are large, and the possibility for sustainability is equally remarkable. Deciphering the fundamentals of this procedure discloses truth flexibility and possibility of plastic extrusion.
The Basics of Plastic Extrusion Process
While it might appear complex, the basics of the plastic extrusion process are based on relatively straightforward principles. It is a production process wherein plastic is thawed and then formed right into a continual account via a die. The plastic extrusion process is thoroughly utilized in various sectors due to its cost-effectiveness, versatility, and efficiency.
Different Types of Plastic Extrusion Strategies
Building upon the standard understanding of the plastic extrusion procedure, it is required to discover the different strategies associated with this production method. Both primary methods are profile extrusion and sheet extrusion. In profile extrusion, plastic is melted and created right into a constant account, typically made use of to create pipes, poles, rails, and home window frames. On the other hand, sheet extrusion develops large, flat sheets of plastic, which are commonly further processed right into items such as food packaging, shower curtains, and car components. Each strategy requires specialized machinery and exact control over temperature level and pressure to ensure the plastic keeps its shape throughout cooling. Understanding these strategies is vital to utilizing plastic extrusion properly in modern manufacturing.
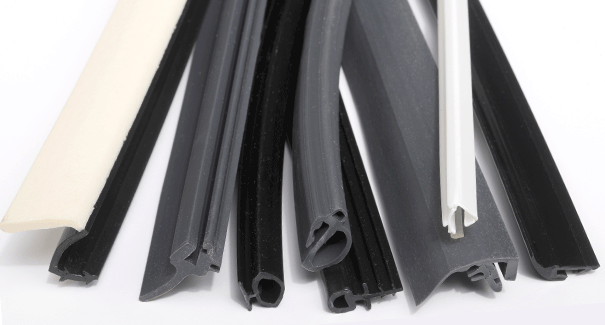
The Function of Plastic Extrusion in the Automotive Sector
A frustrating bulk of parts in modern lorries are items of the plastic extrusion process. This process has actually reinvented the vehicle market, changing it right into a much more efficient, affordable, and adaptable manufacturing sector. Plastic extrusion is mostly made use of in the manufacturing of numerous automobile components such as bumpers, grills, door panels, and control panel trim. The procedure offers an attire, constant result, allowing manufacturers to create high-volume parts with great accuracy and minimal waste. The agility of the extruded plastic parts adds to the overall decrease in car weight, improving fuel effectiveness. Additionally, the resilience and resistance of these components to warmth, chilly, and influence enhance the durability of autos. Therefore, plastic extrusion plays a critical duty in vehicle manufacturing.

Applications of Plastic Extrusion in Customer Item Manufacturing
Beyond its significant impact on the automotive industry, plastic extrusion shows similarly reliable in the realm of durable goods manufacturing. This procedure is crucial in producing a vast selection of items, from food packaging to home home appliances, toys, and even clinical gadgets. The versatility of plastic extrusion allows producers to design and produce intricate sizes and shapes with high precision and efficiency. Due to the recyclability of several plastics, squeezed out elements can be recycled, minimizing waste and cost (plastic extrusion). The flexibility, adaptability, and cost-effectiveness of plastic extrusion make it a preferred choice for many durable goods suppliers, contributing substantially to the market's growth and technology. The environmental effects of this prevalent use need careful consideration, a topic to be talked about further in the succeeding section.
Ecological Effect and Sustainability in Plastic Extrusion
The prevalent use plastic extrusion in manufacturing invites scrutiny of its ecological ramifications. As a process that frequently makes use of non-biodegradable products, the environmental influence can be considerable. Power consumption, waste manufacturing, and carbon exhausts are all worries. Market developments are enhancing sustainability. Effective equipment minimizes visit this page power usage, while waste administration systems recycle scrap plastic, reducing raw material demands. Additionally, the development of naturally degradable plastics uses an extra eco-friendly alternative. Despite these enhancements, better development is required to minimize the ecological impact of plastic extrusion. As culture leans in the direction of sustainability, makers should adjust to remain sensible, stressing the significance of continual research study and advancement in this field.
Final thought
In conclusion, plastic visit site extrusion plays a critical duty in modern manufacturing, especially in the automobile and consumer items industries. Comprehending the essentials of this procedure is key to optimizing its advantages and applications.

The plastic extrusion process is extensively utilized in numerous industries due to its cost-effectiveness, adaptability, and performance.
Structure upon the basic understanding of the plastic extrusion process, it is essential to explore the different methods involved in this production approach. plastic extrusion. In contrast, sheet extrusion develops big, flat sheets of plastic, which are generally further refined into see post items such as food product packaging, shower curtains, and auto components.A frustrating bulk of components in contemporary lorries are items of the plastic extrusion process
Comments on “Plastic extrusion for detailed profiles and custom designs”